Heterojunction technology (HJT) is a not-so-new solar panel production method that has really picked up steam in the last decade. The technology is currently the solar industry’s best option to increase efficiency and power output to their highest levels. HJT combines the best qualities of crystalline silicon with those from amorphous silicon thin-film to produce a high-power hybrid cell that surpasses the performance of the industry’s go-to technology, PERC.
HJT’s latest headline grab came in May when REC Group announced the industry’s most powerful 60-cell solar panel at 380 W, a feat made possible by HJT processes perfected by equipment manufacturer Meyer Burger, an HJT market leader since 2010. As the only equipment supplier offering a turnkey HJT manufacturing process, Meyer Burger is setting up a movement — the company supplied equipment to EkoRE’s under-construction 1-GW HJT line in Turkey as well as SolarTech Universal’s line of HJT panels produced in Florida, and an unnamed North American solar cell startup plans to use Meyer Burger’s HJT technology as it ramps up.
Other large Asian names are going all-in on HJT on their own. Jinergy was one of the first companies to commercialize HJT modules in China and announced in March 2019 that it has reached 23.79% efficiency on its HJT cells, and its 72-cell JNHM72 module reached 452.5 W. Risen Energy broke ground on a 2.5-GW HJT cell and module manufacturing plant in China in August 2019 that should be completed in 2021.
The 2019 “International Technology Roadmap for Photovoltaic” report expects HJT cells to gain a market share of 12% in 2026 and 15% by 2029 — a steady rise for a technology that just a decade ago was only used by Panasonic.
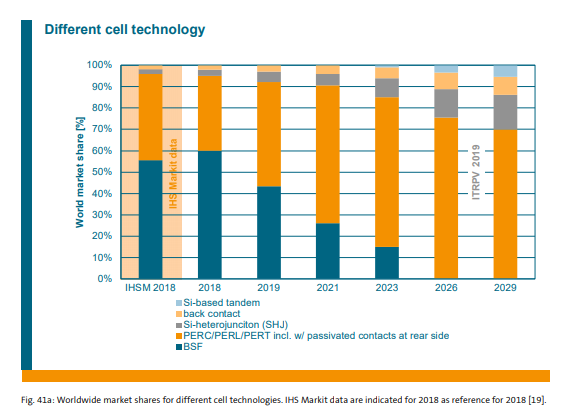
The gray portions of the bars show heterojunction technology’s share of the market. Source: 2019 International Technology Roadmap for Photovoltaic
The HJT production concept was developed by SANYO Electric in the 1980s (SANYO was acquired by Panasonic in 2009). SANYO was the first company to commercially produce solar cells made of amorphous silicon (a-Si). This thin-film technology, most commonly found in pocket calculators, absorbs a wide range of the light spectrum but has a low conversion efficiency (the highest efficiency on record for a-Si is 13.6%). So, SANYO played with a-Si cells, eventually laminating them with crystalline silicon wafers and a transparent conducting oxide (TCO) layer. The c-Si component brought increased efficiency stability while the a-Si side included the increased light absorption. Heterojunction technology was born.
SANYO marketed its HJT modules under the brand name HIT (Heterojunction with Intrinsic Thin-layer technology), which Panasonic still uses today. The first HIT modules, released in 1997, were 14.4% efficient and produced 170 W. Panasonic’s latest 96-cell HIT models average around 20% efficient and produce over 330 W.
Meyer Burger and other solar equipment vendors jumped on the HJT bandwagon after SANYO/Panasonic’s patents on the HIT technology expired in 2010. Dan Glaser, an engineer at Panasonic Life Solutions of America, said Panasonic embraces the industry’s support of its original technology.
“Increasing the manufacturing capacity and R&D resources for heterojunction technology will be excellent for all downstream customers. It will only help to lower costs, increase efficiency and improve reliability,” Glaser said. “We welcome and encourage others to embrace heterojunction technology because of its potential to create a better life for individual customers as well as a better world.”
Meyer Burger has emerged as a leader in HJT because of its continuously tested manufacturing process. Its HJT fabrication equipment uses lower temperatures and less energy than traditional manufacturing lines — an important qualification for perfect HJT end-products. The delicacy lies with the TCO layer that essentially bonds the a-Si and c-Si wafers together. The TCO deposition must not be too hot to affect the sensitive a-Si layer.
Expect more companies to jump on the HJT bandwagon as they weigh the decision to update existing PERC lines or go in a completely different direction. The HJT manufacturing process uses four fewer steps than traditional PERC, so there is room for significant cost savings after initial startup. And the potential power and efficiency gains are even greater.
Panasonic’s Glaser said the company is sticking with heterojunction technology because it often leads to a lower levelized cost of electricity — meaning higher customer satisfaction.
“One of the advantages of HIT is its low temperature coefficient. By having a lower temperature coefficient than other modules, we find that HIT can produce more energy over the life of the system than a module of similar nameplate wattage,” he said. “This ultimately can save a consumer thousands of dollars over the life of the system.”
Happy New Year Kelly. Into a new decade.
You wrote Jinergy’s JNHM72 HJT cells of 2019 puts out 452.5 W with 72 cells at, I surmise 23.79% efficiency.
So: 452.5 W÷72 cells = 6.28 W per cell
At 23.79%
However, a few paragraphs further in the article you write that Panasonic’s latest HJT puts out 330 W from 96 cells at 20% efficiency.
So: 330 W÷96 cells = 3.44 W per cell
At 20% efficiency
How can Panasonic’s latest HJT have specs that are awful compared to Jinergy’s? This is outdated performance.
Please explain.
Thank you
Chris
Panasonic’s 96-cell modules are equivalent to traditional 60-cell modules. So Jinergy’s 72-cell module has 452-W output, while Panasonic’s 60-cell-equivalent module has 330-W output. “Awful” is really up to you.
Hi Kelly.
But you state Panasonic’s latest HJT 96 cell puts out 330 W. “Awful” is backed up by basic arithmetic and 3.44 W per cell is “,awful” compared to 6.28 W per cell. I’m just the messenger of the message, numbers don’t lie.
Besides, in your reply you referred to the Panasonic’s latest HJT as a 60 cell. Even with less cells it’s at 5.5 W per cell. Much better than 3.44 W per cell but still lags behind Jinergy. Not that impressive being it’s their latest HJT panel.
Question: Is the Panasonic’s latest HJT 96 cell or 60 cell?
Thank you
Chris
Chris, Panasonic’s cells are a different size.
I think you all are out to lunch! You can’t compare electrochemical power devices based upon number of cells, or cell power, without knowing cell size. The reason for this is simple, the voltage per cell is the same regardless of size, what changes is the current, and there is a direct relationship between current and ASR, which results in the difference in efficiency and losses due to resistance.
In all electrochemical devices it is always more advantageous to have smaller cells, because you get the voltage for free, and you have higher efficiency and less resistive losses.
For example, I can have 1 cell with 1 volt and if I have 100 amps I then have a 100 watt cell. If I divide that 1 cell into 100 cells, then I have 100 volts so I only need 1 amp to produce 100 watts. V=IR so the more current the more losses due to resistive heating, that’s why power is transmitted at high voltage, your normal high power transmission line may only have a few amps, but you would never transmit the power low voltage and high current the losses would be so great that the transport efficiency would be close to zero and the heat generated due to resistance would destroy the power line.
Dear Kelly,
Also let me remind you about Hevel Group from Russia. We are HJT manufacturer with 10-year experience in thin-film and HJT modules production and operating 270 MW/year manufacturing facility in Russia. Our product range features both HJT monofacial and and double-glass modules with efficiency reaching up to 20%
Hello Kelly,
You have forgotten us !!! Ecosolifer in Hungary. We ordered the first 100 MW heterojunction turn key solar cell production line from Meyer Burger.
We are in operation and from 1 – 1 – 2020 at full capacity.
Open for business !!!